Recovery of Gold and Silver from Anode Slime
Recovery of Gold and Silver from Anode Slime Systeme efficient extraction of precious metals from anode mud, with precise separation and recovery of gold, silver, and other precious metals.
What is Anode Slime?
Anode slime is a sludge-like material that adheres to the anode surface, settles at the bottom of electrolytic cells, or remains suspended in the electrolyte during the electrolytic refining process. It is highly enriched with precious metals, rare metals, and other valuable metals. Extracting these metals from anode slime offers significant economic benefits. For example, copper anode slime can be processed to recover copper and extract elements such as gold, silver, selenium, and tellurium.
Anode Slime Treatment Methods
1. Pyrometallurgical Treatment of Anode Slime
Traditionally, precious metals are recovered by pyrometallurgically removing impurities to concentrate the valuable metals, followed by one or multiple rounds of electrolytic refining.
2. Hydrometallurgical Treatment of Anode Slime
Hydrometallurgical processing involves aqueous solutions for both impurity removal and the extraction of gold and silver. This method essentially combines base metal removal with silver and gold separation steps (e.g., for copper, lead, or crude tin electrolysis anode slimes). The primary objectives are to recover precious metals (Au, Ag), valuable metals (Se, Bi, Te), and return the base metal to the main process stream.
In recent years, hydrometallurgical processes for anode slime have advanced significantly. Treatment has largely shifted from traditional pyrometallurgical routes to predominantly hydrometallurgical flowsheets.
Recovery of Gold and Silver from Anode Slime Process Flow
Full Hydrometallurgical Process for Lead Anode Slime
This process is suitable for materials with high gold and silver content. Lead anode slime, which oxidizes readily, undergoes natural oxidation or roasting at 120-150°C. This converts copper, arsenic, antimony, and bismuth into their respective oxides. The oxidized slime is then leached in an acidic chloride medium to dissolve base metals (Cu, Sb, Bi, As), further enriching the gold and silver content. The de-based slime undergoes chlorination leaching for gold. Simultaneously, any silver not converted to AgCl during oxidation is oxidized. Silver is subsequently leached using a suitable solvent.
Full Hydrometallurgical Process for Copper Anode Slime
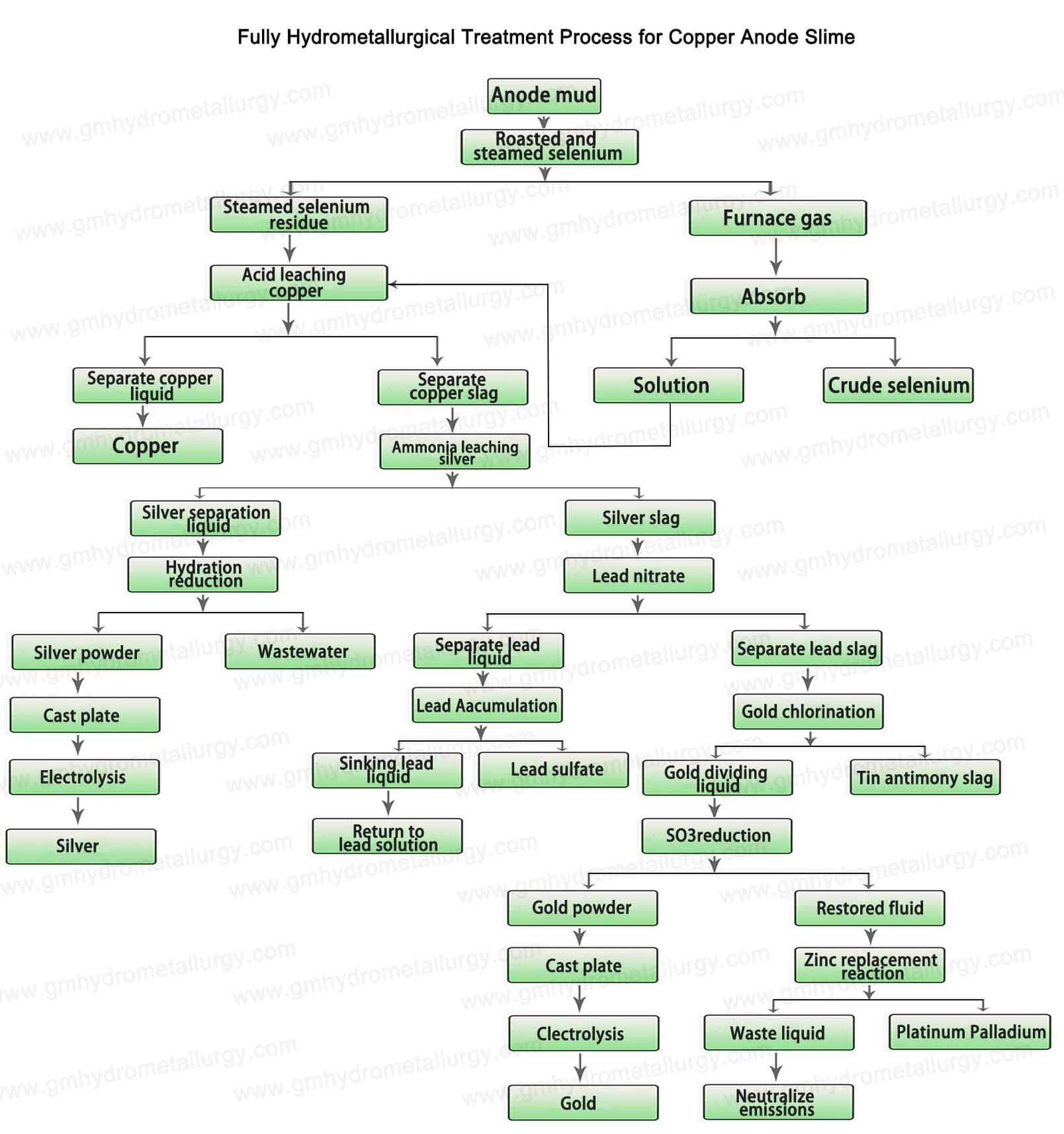
Hydrometallurgical treatment of copper anode slime, like traditional pyrometallurgy, involves separating base metals first, followed by precious metal extraction. Some process stages are similar, such as sulfation roasting of copper anode slime and acid leaching for copper removal.
Pyrometallurgical Route
After decopperization and deselenization, the slime undergoes noble lead smelting and chlorination refining to produce doré metal. The doré is then electrolytically refined to produce pure gold and silver.
Hydrometallurgical Route
The predominant flowsheet involves sulfation roasting for selenium volatilization, leaching for copper and silver removal, and chlorination for gold dissolution. The resulting gold and silver are purified chemically, eliminating the need for separate electrolytic refining steps for these metals.
In recent years, hydrometallurgical processes for anode slime have advanced significantly. Treatment has largely shifted from traditional pyrometallurgical routes to predominantly hydrometallurgical flowsheets.
Raw Material&Final Product
Equipment Advantages
1. High Recovery Rates (>99%)
Direct recovery rates for gold and silver are typically 97-98%, and can exceed 99%, significantly higher than traditional routes.
2. Short Production Cycle
Generally 10-20 days. Gold and silver inventory is lower compared to traditional processes.
3. Suitable for Various Scales
Hydrometallurgical processes are adaptable to anode slime treatment plants of all sizes, particularly small and medium enterprises. Traditional pyrometallurgy requires a certain scale for operational efficiency.
4. Fewer Steps & Shorter Flowsheet
The hydrometallurgical process produces high-purity gold or silver powder directly, which can be melted into anodes for electrolytic refining. Solvent extraction refining of gold chloride solutions can yield Grade 1 gold, completely bypassing the gold electrolysis step.
5. No Intermediate Recycling Streams
The hydrometallurgical process replaces smelting and silver refining furnaces with separate gold and silver leaching steps. This eliminates the production of intermediate recycling streams (accounting for 30-40% of the slime feed), improving direct recovery and reducing costs.
6. Enhanced Comprehensive Utilization
During base metal separation, valuable metals are concentrated at high ratios in specific residues or solutions, facilitating efficient comprehensive recovery.
Technical Parameter
Anode Slime Hydrometallurgical Refining System Technical Parameters
If you have other requrement and want to know more details, please contact us.(The data in this table are for reference only)
Model | Capacity kg/day | Power/kw | Size(Length*Width*Height) | Project Budget(USD) |
PGM-100 | 100-200kg | 300kw | 10000*5500*6000mm | 150000USD |
PGM-300 | 300-500kg | 500kw | 15000*8500*6000mm | 200000USD |
PGM-500 | 500-1000kg | 800kw | 20000*15000*7000mm | 500000USD |
PGM-1000 | 1000-2000kg | 1000kw | 35000*20000*7000mm | 1000000USD |
Our Services
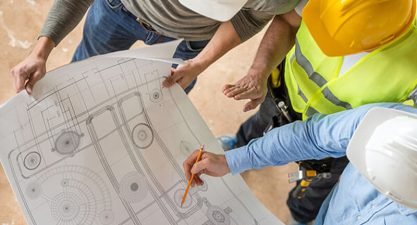
Production Flow Diagram
Complimentary provision of production flow diagrams and installation foundation drawings for buyer-required equipment.

Site Layout
Free adjustment services for layout plans during the entire operational process, provided upon buyer request.
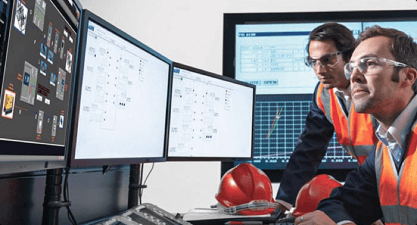
Installation Training
During installation and trial operation, our engineers will be dispatched on-site for equipment installation, commissioning, and necessary operational training.

Accessories Supply
A list of wear-prone and consumable parts is provided. Spare parts are sold at factory prices when purchased directly from Guanma Machinery.
Contact Us
Please specify your requirement by referring to the following aspects:
1-What type of precious metal do you want to extract?
2-How many tons raw material do you want to process per kg?
3-When will you want to start this project?
4-How is your budget of machine?
5-Which point that you really focus on?(We have customized service for each client)