The oxygen-enriched side-blowing furnace includes waste heat boiler, surface cooler, bag dust collector, waste heat power generation, desulfurization and other systems.
The basic task of the oxygen-enriched side-blowing furnace reduction smelting is to reduce the liquid high-lead slag produced by the bottom-blowing furnace to produce crude lead, zinc-containing slag, and sulfur-containing flue gas. The zinc-containing slag enters the fuming furnace for further blowing, and the sulfur-containing flue gas enters the desulfurization system after dust collection.
Oxygen Enriched Side-Blown Furnace Process Flow
Guanma Machinery Oxygen Enriched Side-Blown Furnace operates as a highly efficient submerged bath smelter:
Feed Preparation & Charging
Feedstock (concentrates, secondary materials) is blended with fluxes (SiO₂, CaO, Fe) and reductant (if needed).
Prepared mix is continuously fed into the furnace via feed ports (roof/side).
Intense Smelting & Reaction Zone
High-purity oxygen is injected horizontally through side tuyeres directly into the molten bath beneath the slag layer.
Intense Reactions Occur
Combustion: Generates intense heat (1200-1300°C).
Oxidation: Sulphides oxidize (e.g., 2FeS₂ + 5.5O₂ → Fe₂O₃ + 4SO₂ + Heat).
Reduction: Oxides are reduced to metal (e.g., PbO + CO → Pb + CO₂).
Fluxing: Impurities form a liquid slag (FeO-SiO₂-CaO dominant).
Phase Separation & Tapping
Dense molten metal (matte, bullion, alloy) settles to the furnace bottom.
Less dense slag floats above the metal phase.
Metal phase is tapped intermittently/continuously from the lower tap-hole.
Slag is tapped separately from a higher elevation. Slag composition is controlled for disposal or valorization.
Off-Gas System – Critical for Emissions Control
High-temperature, SO₂-rich flue gas exits the furnace.
Waste Heat Recovery: Gas passes through a boiler generating steam/power.
Gas Cooling & Dedusting: Cooled gas undergoes multi-stage cleaning (Cyclones → ESP or Baghouse).
Sulfur Capture: Cleaned, high-strength SO₂ gas feeds a sulfuric acid plant.
Final Emission Control: Treated gas meets global emission standards before release.
Raw Material & Output
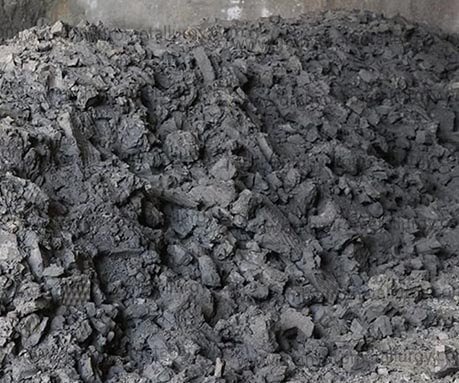
Lead Concentrate
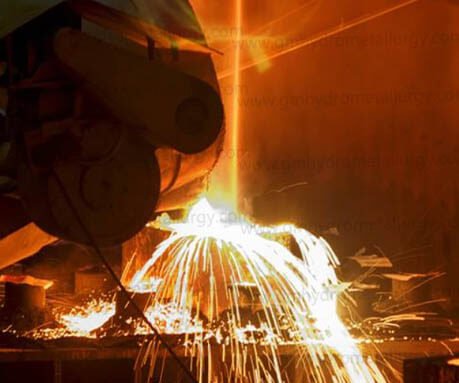
Crude Tin
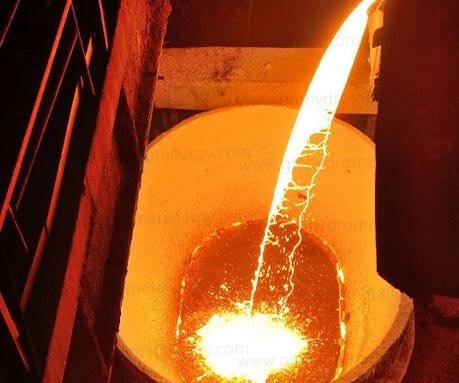
Crude Lead
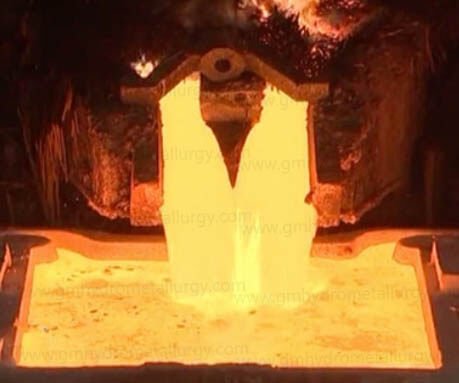
Crude Copper
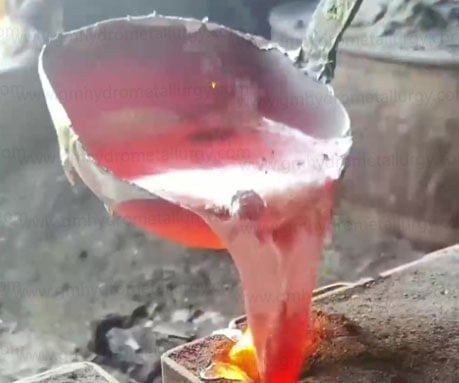
Crude Antimony
Raw Materials: Copper concentrate, Blister copper, Lead concentrate, Spent lead-acid battery paste & grids, Crude lead ingots, Nickel sulfide concentrate, Cassiterite (tin ore) concentrate, E-waste, Spent catalysts (containing Cu, Al, Pb, Zn, Sb, Sn, etc.)
Final Products (Minimum Purity ≥95%): Crude copper, Crude aluminum, Crude lead, Crude zinc, Crude antimony, Crude tin.
Equipment Advantages
Why Choose Guanma's Oxygen Enriched Side-Blown Furnace?
Highest Metal Recovery (>98%)
Maximize yield and profitability from valuable primary and secondary resources.
Dramatically Lower Operating Costs
Reduced energy consumption (fuel + power) and lower reagent costs due to high thermal efficiency.
Environmental Performance
Ultra-Low Emissions: >99.5% SO₂ capture, minimized NOx/CO/dust, negligible dioxins/furans.
Stable, Non-Hazardous Slags: Compliant with strict disposal regulations globally.
Unparalleled Feedstock Versatility
Process virtually any metal-bearing concentrate or complex secondary/residual material efficiently.
Superior By-Product Value
Generate high-value slags (e.g., high-Zn for Zn recovery) or mattes (PGM enrichment).
Process Robustness & High Availability
Simple operation, robust refractory design, and easy tuyere maintenance ensure maximum uptime.
Fuel & Oxygen Flexibility
Adapt to local fuel economics and optimize oxygen usage for cost and performance.
Proven Technology & Guanma Innovation
Based on robust bath smelting principles, enhanced with Guanma Machinery proprietary tuyere cooling, refractory lining, and process control systems for peak performance and longevity.
Scalability & Modularity
Furnace design tailored precisely to your capacity needs, from small recyclers to large primary smelters.
Full Lifecycle Support
Guanma Machinery provides end-to-end partnership: feasibility studies, process engineering, detailed design, supply, installation supervision, commissioning, operator training, spare parts, and ongoing technical service.
Technical Parameter
Oxygen Enriched Side-Blown Furnace Technical Parameters
If you have other requrement and want to know more details, please contact us +86 17838366846.(The data in this table are for reference only)
Capacity | 300 ton/day | 500 ton/day | 1000 ton/day |
Raw Materials | Non-ferrous metal feedstocks containing lead (Pb), zinc (Zn), copper (Cu), antimony (Sb), tin (Sn), etc. | ||
Size | 3.5 m³ | 5.5 m³ | 11 m³ |
Power | Custom-designed based on material properties | ||
Product Purity | ≥95% | ||
Recovery Rate | ≥99% | ||
Heating Methods | 60-200m³/h,Two Burners/Furnace | ||
Smelting Temperature | 10-30 t/h | ||
Smelting Duration | 5-20m³/h |
Our Services
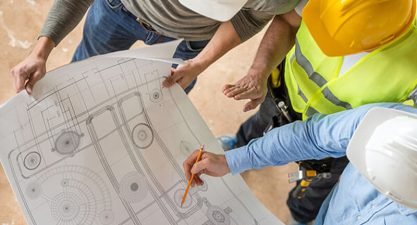
Production Flow Diagram
Complimentary provision of production flow diagrams and installation foundation drawings for buyer-required equipment.

Site Layout
Free adjustment services for layout plans during the entire operational process, provided upon buyer request.
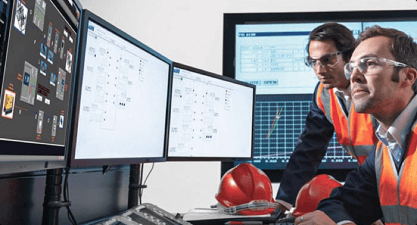
Installation Training
During installation and trial operation, our engineers will be dispatched on-site for equipment installation, commissioning, and necessary operational training.
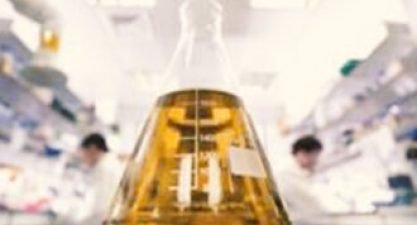
Sample Testing
According to the customer's raw materials, test and send the final sample product. come out testing report to help clients analyze the project.

Accessories Supply
A list of wear-prone and consumable parts is provided. Spare parts are sold at factory prices when purchased directly from Guanma Machinery.
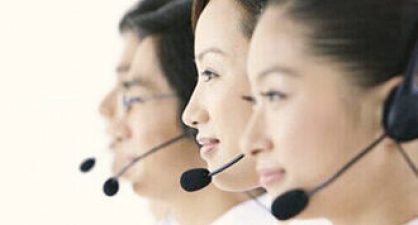
Technical Upgrade Support
Technical updates for equipment are available throughout the production cycle. If clients request upgrades, only material costs will be charged.
Contact Us
Please specify your requirement by referring to the following aspects:
1-What type of precious metal do you want to extract?
2-How many tons raw material do you want to process per kg?
3-When will you want to start this project?
4-How is your budget of machine?
5-Which point that you really focus on?(We have customized service for each client)