Copper Electrolytic Refining Machine Manufacturer primarily employs two methods: pyrometallurgical refining and electrolytic refining. The electrolytic refining method is generally preferred, as it can elevate the copper grade to over 99.95% while recovering valuable elements from pyrometallurgically refined copper, particularly precious metals, platinum-group metals, and rare/scattered metals.
The cathode copper grade produced by fire refining is generally 99.2~99.7%, which also contains 0.3~0.8% impurities. In order to improve the performance of copper to meet the requirements of various applications and recover the valuable metals, especially precious metals, platinum group metals and rare metals, it must be electrolytically refined.
Copper Electrolytic Refining Process Flow
Copper electrolytic refining typically involves several key steps: anode processing, starter sheet production, electrolysis, electrolyte purification, and anode slime treatment. The main process flow is as follows:
1. Starter Sheet Production
In the starter cell, anodes produced via pyrometallurgical refining are used as anodes, while pure copper or titanium mother blanks (now commonly adopted) serve as cathodes. Direct current at a specific current density is applied, causing the anode copper to dissolve electrochemically and deposit pure copper sheets onto the mother blanks. These thin pure copper sheets are called starter sheets. After being peeled off the mother blanks, they undergo flattening, embossing, lug attachment, and other processing steps to become cathodes for production cells.
2. Anode Processing
Anodes are prepared for installation by milling lugs, flattening (or hammering), removing burrs and edges, and correcting plate flatness.
3. Electrolysis Process
In production cells, the anodes and starter sheets undergo electrolysis to yield the final product: cathode copper (or electrolytic copper).
4. Electrolyte Purification
The electrolyte is periodically circulated through a purification system to remove accumulating copper ions and eliminate excessive impurities such as nickel, arsenic, antimony, and bismuth.
Raw Material&Final Product
The primary raw materials for copper electrolytic refining include blister copper, copper ore, scrap copper wires, scrap copper foils, scrap copper conductors, and copper scraps. The final products obtained through this process are electrolytic copper, refined copper, copper rods, copper bars, copper tubes, copper strips/sheets, and copper foils.
Equipment Advantages
High-Efficiency Purification
Swirl Electrolysis Technology: Enhances mass transfer, increasing cathode copper ion concentration by 30-50%. Maintains high recovery efficiency even when processing low-grade ores.
Environmental Sustainability & Energy Savings
Electrolyte reuse: Reduces wastewater discharge. Acid mist recovery systems: Ensure harmful gas emissions meet environmental standards.
PLC Intelligent Control
Real-time monitoring of parameters such as current efficiency and electrolyte pH. Automated adjustment of additive dosing for optimal process stability.
High-Purity Output
Cathode copper purity: Up to 99.99%, meeting demands for high-conductivity materials in applications like new energy vehicles.
Resource Circularity
Recovery of precious metals (e.g., gold, silver) from anode slime. Full utilization of waste residues to achieve zero-residue resource recovery.
Technical Parameter
Copper Electrolytic Refining Machine Technical Parameters
Working voltage can be customized, and if you have other requrement and want to know more details, please contact us.(The data in this table are for reference only)
Model | Mixed Metal Powder | Energy Consumption(KWH) | Electrolytic Cycle(Anode/Cathode) | Copper Capacity | Copper Purity |
CER-500 | 500kg/day | 280 | 15days/48h | 370 | 99.9% |
CER-1000 | 1000kg/day | 570 | 15days/48h | 750 | 99.9% |
CER-2000 | 2000kg/day | 1130 | 15days/48h | 1500 | 99.9% |
CER-5000 | 5000kg/day | 2850 | 15days/48h | 3750 | 99.9% |
Our Services
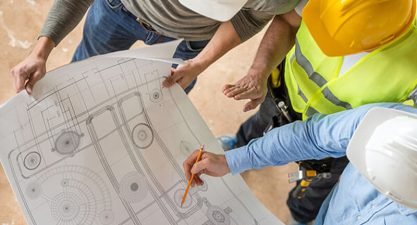
Production Flow Diagram
Complimentary provision of production flow diagrams and installation foundation drawings for buyer-required equipment.

Site Layout
Free adjustment services for layout plans during the entire operational process, provided upon buyer request.
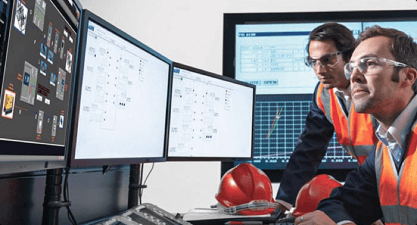
Installation Training
During installation and trial operation, our engineers will be dispatched on-site for equipment installation, commissioning, and necessary operational training.
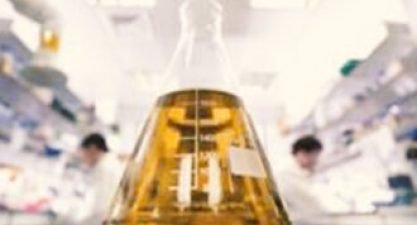
Sample Testing
According to the customer's raw materials, test and send the final sample product. come out testing report to help clients analyze the project.

Accessories Supply
A list of wear-prone and consumable parts is provided. Spare parts are sold at factory prices when purchased directly from Guanma Machinery.
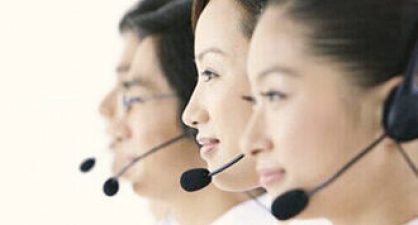
Technical Upgrade Support
Technical updates for equipment are available throughout the production cycle. If clients request upgrades, only material costs will be charged.
Contact Us
Please specify your requirement by referring to the following aspects:
1-What type of precious metal do you want to extract?
2-How many tons raw material do you want to process per kg?
3-When will you want to start this project?
4-How is your budget of machine?
5-Which point that you really focus on?(We have customized service for each client)