Precious Metal Extraction from Lead-Zinc Ores Solutions
Precious Metal Extraction from Lead-Zinc Ores transforms overlooked byproducts into high-value revenue streams. While lead and zinc constitute primary commodities, trace amounts of gold, silver, platinum group metals (PGMs), and indium often report to tailings or smelting residues – representing significant untapped profit potential.
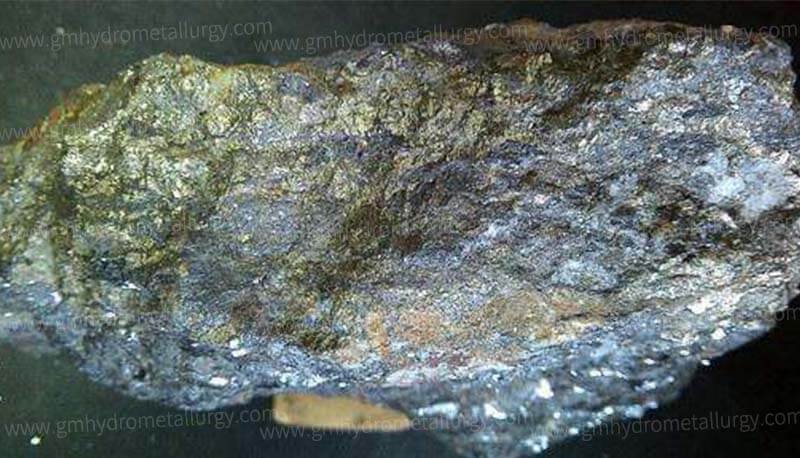
Lead-Zinc Ores
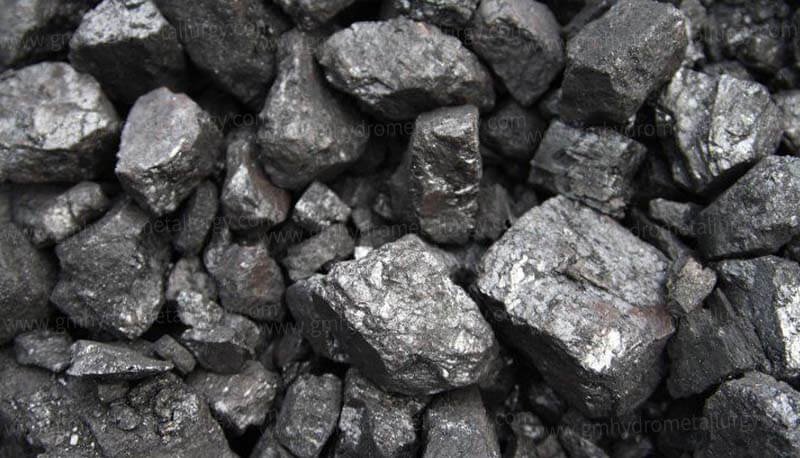
Lead-zinc Ore
Why Recover Precious Metals from Lead-Zinc Ores?
Economic Imperative: Au/Ag/PGMs can contribute 15-30% of total ore value.
Resource Optimization: Mitigate supply chain risks for critical minerals.
ESG Compliance: Prevent toxic metal migration (e.g., cadmium, arsenic).
Feedstock Diversification: Process historical tailings via precious metal recovery from zinc leach residues.
Precious Metal Extraction from Lead-Zinc Ores Process
Precious Metal Occurrence & Pre-Concentration
1. Host Mineralogy
Silver occurs as cerargyrite (AgCl), native silver, argentite (Ag₂S).
Gold associates with sulfide minerals.
Significant solubility variations exist (e.g., cyanide-soluble cerargyrite vs. refractory pyrargyrite).
2. Pre-Concentration Technologies
Flotation Methods
Differential Flotation: Zinc mineral depression with selective silver-bearing galena recovery (leveraging silver’s affinity for lead).
Bulk Flotation: Co-flotation of Pb-Zn-Ag followed by separation/direct smelting.
Split/Asynchronous Flotation: Reagent optimization for complex ores (enhances Ag recovery).
Heap Leaching (Oxide Ores).
Smelting & Extraction Metallurgy
1. Pyrometallurgical Concentration
>95% precious metals report to crude lead during smelting. Subsequent electrolytic refining concentrates >99% PMs in lead anode slime.
2. Anode Slime Processing
Pyrometallurgical-Electrochemical Route
Anode slime smelting → Cupellation → Electrorefining of Au-Ag alloy → Silver/Gold ingot production.
Hydrometallurgical Route
Chloride leaching (base metal removal) → Ammoniacal silver dissolution → Chemical reduction to silver powder.
Hybrid Processing
De-arsenication/de-antimonization → Smelting → Granulation → Hydrometallurgical PM recovery.
Stop losing precious metal revenue to tailings! Our metallurgical engineers will audit your ore/residues to design customized extraction circuits – boosting profitability while reducing environmental liabilities. Guanma Machinery, a professional supplier of precious metal recycling equipment, offers tailored solutions. Get a tailored solution and quote now!
Process Economics & Application Matrix
Process Economics & Application Matrix
Method | Ore Type | Competitive Advantages |
Flotation | Sulfide Ores | High Ag upgrade ratio (Pb concentrate) |
Cyanide Heap Leach | Oxide/Porous Ores | Low CAPEX, operational simplicity |
Pyro-Electro | High-Ag Anode Slime | >99% recovery, proven technology |
Hydrometallurgy | Low-PM feeds/EPZ | Zero gas emissions, multi-metal recovery |
Note: Process selection requires ore mineralogy analysis and economic evaluation. |
Our Services
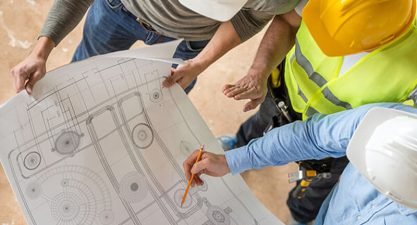
Production Flow Diagram
Complimentary provision of production flow diagrams and installation foundation drawings for buyer-required equipment.

Site Layout
Free adjustment services for layout plans during the entire operational process, provided upon buyer request.
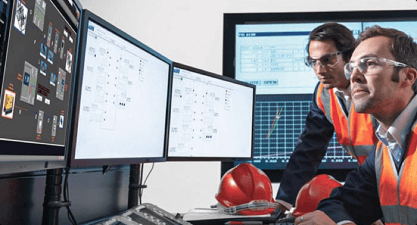
Installation Training
During installation and trial operation, our engineers will be dispatched on-site for equipment installation, commissioning, and necessary operational training.

Accessories Supply
A list of wear-prone and consumable parts is provided. Spare parts are sold at factory prices when purchased directly from Guanma Machinery.
Contact Us
Please specify your requirement by referring to the following aspects:
1-What type of precious metal do you want to extract?
2-How many tons raw material do you want to process per kg?
3-When will you want to start this project?
4-How is your budget of machine?
5-Which point that you really focus on?(We have customized service for each client)